黎明数字化制造技术应用纪实
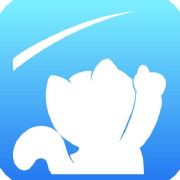
看航空
核心提示:在工艺参数优化方面,采用了基于均衡切削载荷策略的工艺参数优化方法,有效解决了零件加工变形、加工颤振和刀具磨损等生产瓶颈问题,经过现场实际加工验证,单片叶片精铣加工效率提高约30%,加工质量也大幅提高。
中国航发黎明数字化制造专业始终跟随前沿技术发展,开展数字化制造技术研究,致力于以技术创新谋求发展。凭借多年技术研发的积累沉淀,以务实、创新为主旋律,紧密围绕航空产品工艺研发主线,充分发挥数字化制造专业优势,引领公司以及行业内的持续发展。
夯实基础——持续探索新思路
随着制造技术向全面数字化方向发展,中国航发黎明始终坚持面向现场用户的工作理念,前瞻性地进行技术研究储备,在行业内率先提出三维环境下应用MBD(基于模型的定义)方式进行工艺设计,经叶盘、机匣、盘轴等航空发动机典型零件的应用验证,可直接应用于型号研制,成功解决了三维设计数据有效继承并快速进行工艺设计的难题。中国航发黎明数字化制造专业在实现了对工艺源头数据有效控制的基础上,开拓新思路,以工艺创新为引领,继而开展对工艺过程数据的控制研究。
结合航空产品的生产加工特性,在工艺研制过程中反复加工试验和多次修改工艺路线是常规的研发途径,由此产生大量低水平重复操作、试验件消耗,不仅会增加预研产品的试验成本和研制周期,更严重制约了航空发动机研制水平的提高。中国航发黎明数字化制造专业通过对产品工艺过程关键环节的深入研究,从多方因素开展工艺性分析,利用多种数字化仿真技术的集成应用,开展了物理仿真工程化应用研究,充分发挥数字化制造技术在产品各个生产阶段的专业优势。
革故鼎新——科学验证新方法
叶片是航空发动机的关键动力部件之一,对发动机的性能起着至关重要的影响,然而叶片的加工变形与精度控制却一直是制约叶片加工效率和加工质量提升的瓶颈。随着公司叶片产能需求的逐年提升及新结构、新材料、新设备的不断发展,叶片的加工工艺也随之发生适应性改变。如何针对以上问题顺应数字化制造技术和自动化技术的发展趋势,从工艺的合理性、规范性、适应性视角探索出适合叶片高效、优质加工的有效方法是传统机加行业必将面临的转型。
航空发动机叶片制造大多采用精密数控加工技术,一直朝专业化、标准化方向发展。国外的机床厂家、系统集成商、软件系统供应商研发了系列叶片专用数控加工中心、柔性加工单元和数控加工编程软件,并形成了系列化、标准化、专业化配套工艺装备,系列化产品功能和性能不断完善。国外航空企业为争夺市场份额,缩短研制周期,不惜巨额投资,在生产线上配置了一大批高精度数控设备,用于专业化生产线改造,实施计算机辅助设计/制造一体化工程,实现了集成数字化制造。然而国内叶片制造企业的精加工数控设备和编程工具基本被国外供应商所垄断。
中国航发黎明数字化制造专业自2008年起,针对航空发动机轴颈类静子叶片的精准加工理论、工艺方法、关键技术和工艺装备等关键技术领域,通过整合产学研合作资源,连续多年跟踪、跟进国内外叶片加工领域的先进制造技术、先进工艺装备、加工刀具和工业软件的发展历程,立足型号需求持续开展攻关研究。
通过现场跟踪调研叶片实际的加工情况,发现某叶片主要面临加工变形、型面扭曲、加工颤振、刀具磨损严重等问题,通过进行深层次的理论分析,确定设备精度、夹具定位精度和装夹变形、工艺系统刚性、零件材料高硬度带来的冷作硬化现象、切削温度过高是造成叶片加工问题的主要原因,最终决定借助仿真工具从减少切削加工过程中的切削力、抑制振动、提高刀具耐用度三个方面寻求解决途径,在虚拟环境下借助仿真手段对零件设计制造全生命周期的各个环节实现分析、优化,并进行合理的加工验证。
在虚拟环境下,应用先进的仿真工具对叶片的数控加工程序、刀具、装夹方案进行分析优化,并应用正交试验法确定刀具齿数和进给量是影响切削力的主要因素,通过仿真手段确定对刀具进行优化,选用7齿抑振密齿刀代替原有的4齿刀具进行叶片加工,解决了弱刚度叶片易产生的加工振颤、加工变形和刀具寿命低等瓶颈问题。工艺参数优化方面,采用了基于均衡切削载荷策略的工艺参数优化方法,有效解决了零件加工变形、加工颤振和刀具磨损等生产瓶颈问题,经过现场实际加工验证,单片叶片精铣加工效率提高约30%,加工质量也大幅提高。
该型叶片的攻关工作都是在软环境中进行,技术分析、工艺验证和技术决策等均在虚拟加工平台完成,技术风险几乎为零。整个分析工作长达3个月,研制工作长达9个月,但实际零件技术验证时间几乎为零,整个验证工作在技术中心进行。技术中心组建的数字化制造专业的青年技术骨干在无需试验件、无需加工调试、无需抢占生产用设备,未对叶片的正常生产进程造成影响的条件下,实现了验证周期的缩短和试验成本有效降低,为航发叶片研发、叶片高效精准加工的新工艺制定提供了技术可能。
聚焦主业——矢志突破新技术
航空发动机朝着轻质化、高可靠性、长寿命、多构型、快速响应及低成本制造等方向发展,叶片类零件也随之大量采用新材料、新结构、新工艺,仅依靠已有的生产经验与试制验证的传统生产工艺准备方式已然无法满足我国航空制造业快速发展的需求,因此虚拟加工、工艺仿真等技术的应用必将成为叶片加工的必然趋势。
工艺仿真技术是以航空发动机关重零部件研制为主线,针对产品关键工艺过程及其研制过程,持续推进加工过程仿真技术、数字化工厂仿真技术和集成工艺仿真技术应用,在虚拟环境中对生产工艺准备、加工过程、工艺参数和加工结果进行仿真分析,并以精确的仿真结果指导实际的生产过程,以提高现有工艺装备利用率、增加产能。近年来,中国航发黎明紧跟前沿技术发展趋势,突破传统叶片加工技术理念,开展工艺仿真、数字化工厂、虚拟制造等关键技术的研究工作,逐渐形成了覆盖产品生产制造全生命周期各个阶段的仿真技术应用探索,如在生产线建设阶段,拟应用工业工程的方法定义生产线需求和功能,借助工厂设计和优化工具,对生产系统和过程进行建模和仿真,对生产线布局及过程运动的合理性进行评估、优化和调整;在生产准备阶段,借助生产线运行仿真环境模拟真实的生产线运行过程,对人机交互、机器人动作及各制造单元工序能力、瓶颈进行分析和评估,实现生产线的生产能力平衡;在零件加工阶段,借助虚拟仿真和验证工具,预先分析、评估、验证产品装配、零件加工等制造过程,提前发现潜在问题,减少研制风险;在产品检验检测阶段,借助于集成工艺仿真环境,基于产品的设计、工艺、制造等信息模拟产品的制造结果,追溯导致产品质量问题的原因,从而提升产品质量。